If ensuring the smooth operation and longevity of your organisation’s equipment and other facilities is your prime goal, effective maintenance is the best path to walk on. Organisational maintenance is not a simple task. It is actually a long process that consists of interwoven elements from start to finish. This is why an organisation must have a thorough understanding of the ‘maintenance planning process’ in order to execute it properly.
In this article, we cover everything you need to know about the maintenance planning process of a modern organisational setup.
We will reveal
Exploring Maintenance Planning as a Concept
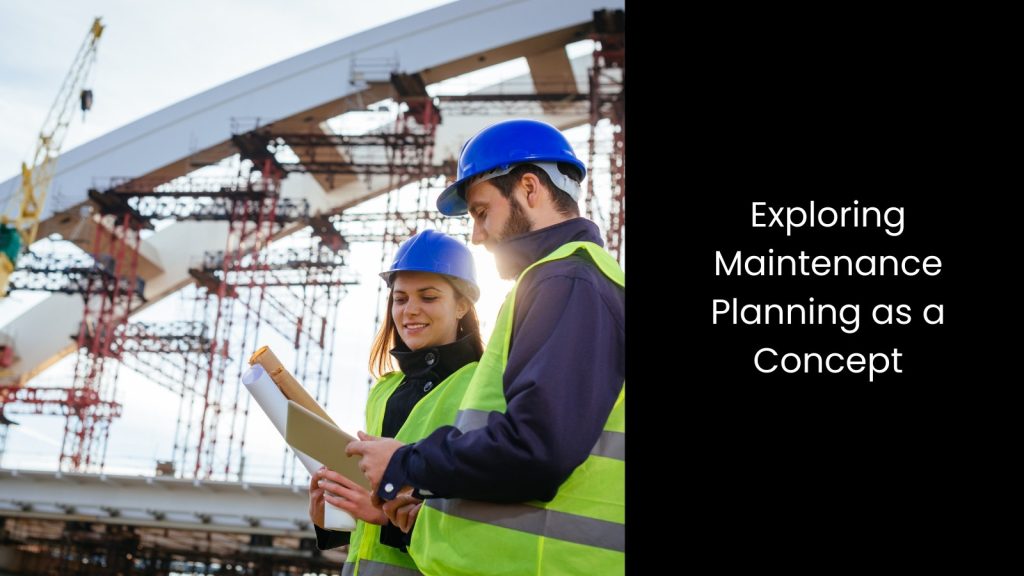
- This is actually a systematic approach used by businesses to ensure that their equipment and facilities remain in good working condition. In the business world, it involves creating a detailed schedule for regular maintenance tasks, such as inspections, repairs, and replacements.
- In a way, this is a proactive approach that helps companies avoid unexpected breakdowns and costly repairs as it addresses potential issues before they become serious problems. If they can plan maintenance activities in advance, businesses can minimise downtime, which is the period when equipment is not operational.
- Maintenance planning also helps companies extend the lifespan of their assets. We all know that regular upkeep ensures that machinery and equipment operate efficiently, reducing the likelihood of premature wear and tear. Furthermore, it improves safety by identifying and fixing hazards before they cause accidents.
- This is why companies need maintenance planning to optimise their resources and manage costs effectively. Without a solid plan, businesses might face unplanned maintenance expenses, which can strain their budgets.
Key 6 Steps in the Maintenance Planning Process

Step 1-Identifying the Problem
This is undoubtedly the first step in the maintenance planning process. It sets the foundation for all subsequent actions.
In order to do this effectively, businesses need to thoroughly examine their equipment and systems to pinpoint what is wrong. Let us explain how. There are many approaches they can opt for to identify problems, including conducting regular inspections, monitoring performance data, and soliciting feedback from operators who use the equipment daily.
As we all know, inspections help detect visible issues or signs of wear and tear, while performance data can reveal anomalies or patterns that indicate underlying problems. However, feedback from operators provides insights into how equipment behaves under normal working conditions and helps spot issues that might not be immediately apparent through other methods.
This is quite challenging, as inaccurate problem identification can lead to incorrect maintenance actions, wasting time and resources. This step is important because it prevents wasting money on unnecessary repairs and avoids potential equipment failures that can cause significant disruptions. Therefore, investing time and resources into accurate problem identification lays the foundation for successful maintenance planning and long-term operational success.
Step 2-Planning Maintenance
Planning maintenance is the second step in the maintenance planning process, where businesses develop a structured approach to address the identified problems.
This is when companies need to establish a detailed schedule that includes specific tasks, resources required, and the timing of each maintenance activity. Maintenance planners usually do this by creating a maintenance calendar, assigning responsibilities to team members, and estimating the time and cost involved for each task.
A maintenance calendar helps in organising tasks and ensuring they are performed regularly while assigning responsibilities clarifies who will carry out each task. However, it is also important to balance maintenance activities with operational demands, as maintenance tasks can disrupt normal production schedules. Businesses must also ensure that they have the necessary parts and tools available, which requires accurate inventory management and supply chain coordination.
Without a clear plan, maintenance activities might be rushed or poorly executed, and it will end up leading to ineffective repairs and higher long-term costs. This is why a company must go with proper planning. The latter ensures that all necessary tasks are completed systematically, improving equipment reliability and extending its lifespan.
Step 3-Scheduling
This is where businesses arrange when and how maintenance activities will take place. However, this is not a simple task. In order to fulfil this responsibility effectively, maintenance planners need to create a timeline that outlines specific dates and times for each maintenance activity based on the priorities set during planning.
This can be done in various ways. They can use maintenance management software to automate and track schedules, set up regular maintenance intervals, or coordinate with different departments to minimise disruptions.
Plus, companies must also consider the availability of staff and resources, as scheduling during busy periods can lead to delays and increased costs. This step ensures that maintenance tasks are performed at the right time, which helps prevent unexpected equipment failures and reduces downtime.
Step 4-Allocating Tasks
This is the fourth step in the maintenance planning process. This is exactly where businesses assign specific maintenance responsibilities to team members. This means matching the right person to each job based on their skills, experience, and availability.
Planners can start this by creating a detailed task list, identifying the required skills for each task, and ensuring that the workload is evenly distributed among team members. Creating a task list helps in organising what needs to be done, while identifying required skills ensures that each task is assigned to someone who can perform it effectively. Distributing the workload evenly prevents overburdening any single team member and promotes efficiency.
Allocating tasks bears a heavy weight as it ensures that maintenance work is carried out efficiently and effectively, helping to maintain equipment reliability and minimise downtime. If there is proper task allocation, it helps in managing resources better, as it allows businesses to utilise their staff’s strengths and manage their time effectively.
In another way, it supports optimising team performance and ensuring that all maintenance activities are completed on schedule. When they match tasks to the right individuals and manage resources efficiently, businesses can enhance operational efficiency and prevent equipment failures.
Step 5- Confirmation of Proper Execution
If all the tasks are properly done, what would be the next step?
Confirmation ensures that all maintenance activities have been completed correctly and effectively. Businesses can do this by conducting inspections, reviewing maintenance records, and obtaining feedback from operators.
This is very important, as sometimes overlooked details or incomplete documentation can lead to missed problems or ineffective maintenance. Another challenge is obtaining honest and detailed feedback from operators, as they might not always report issues or changes clearly. Confirming that maintenance is properly done is the base because it helps in verifying that the maintenance plan was executed correctly, which in turn prevents future equipment failures and prolongs the equipment’s lifespan. It ensures that any potential issues are addressed promptly and that maintenance work meets the required standards.
This is why it is vital to confirm proper maintenance. This way, businesses can maintain high equipment reliability, minimise downtime, and avoid costly repairs or replacements.
Step 6- Analysing Root Causes and Prevention Planning
It is not enough to solve the issue if you cannot identify its root cause. Otherwise, you will not get the chance to stay away from occurring again in the future.
That is why analysing root causes and planning prevention has become the last step in the maintenance planning process. The latter focuses on identifying the underlying issues that caused equipment problems and developing strategies to prevent them from happening again.
How can this be done smoothly? Well, there are certainly multiple ways. For example, businesses can use approaches such as the ‘5 Whys’ technique, root cause analysis (RCA), and failure mode and effects analysis (FMEA). The ‘5 Whys’ technique involves asking ‘why’ repeatedly until the underlying cause of a problem is identified. RCA means systematically investigating the problem to uncover its fundamental causes, while failure mode and FMEA evaluate potential failure points and their impact.
This step can be extensive and complex, yet it helps businesses understand why problems occur, which allows them to develop effective strategies to prevent recurrence. If you can address the root cause, businesses can enhance equipment reliability, improve safety, and reduce long-term maintenance costs.
If the companies fail to understand and eliminate the underlying issues, that will lead to equipment failures beyond doubt. That is why the modern business asset management sector has given much weight to this last step. Prevention planning ensures that companies proactively address issues before they lead to more significant problems, minimising downtime and maintaining smooth operations. This step helps businesses develop effective strategies to prevent future problems, ensuring greater reliability and efficiency in their operations.
Simplifying Maintenance Planning via Cutting-edge Tools
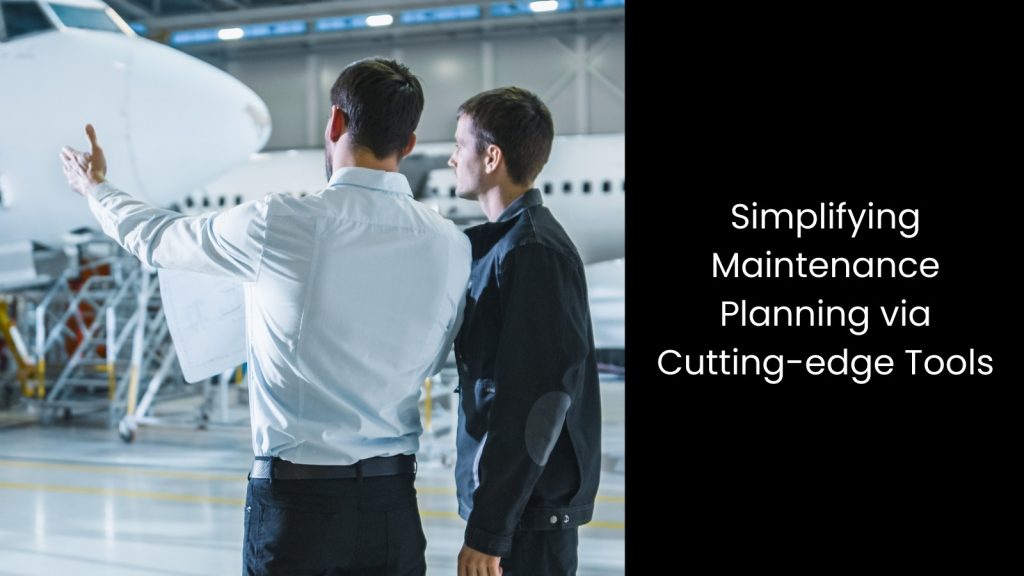
Yes, we agree that maintenance planning is a hectic process. However, there are solutions to simplify it. One of those techniques is using new-age tools and technologies. Integrating cutting-edge tools into maintenance planning transforms traditional practices into streamlined, data-driven processes. The adoption of these advanced solutions ensures more accurate scheduling, proactive issue detection, and efficient resource management. This way, businesses can achieve greater reliability, lower costs, and improved equipment longevity, driving operational excellence. However, it is also important to check the expertise of your software provider before purchasing these tools.