As per the reports, the demand for warehousing in Singapore is expected to grow more than 4% yearly for the next five years. This means we are stepping into an era where efficiency and space optimisation drive a company’s operational success. Although this growth seems promising, Singapore’s warehousing sector might face increasing pressure to adapt and innovate according to the blooming demand. Expanding warehouse operations should start from one particular point. That is ‘warehouse layout design’, which can optimise the limited space in Singapore.
In this article, we explore a few tips to optimise space through a meaningful warehouse layout design, which you can adopt if you run out of land for storing operations.
We will know
Why is Warehouse Layout Design Important?
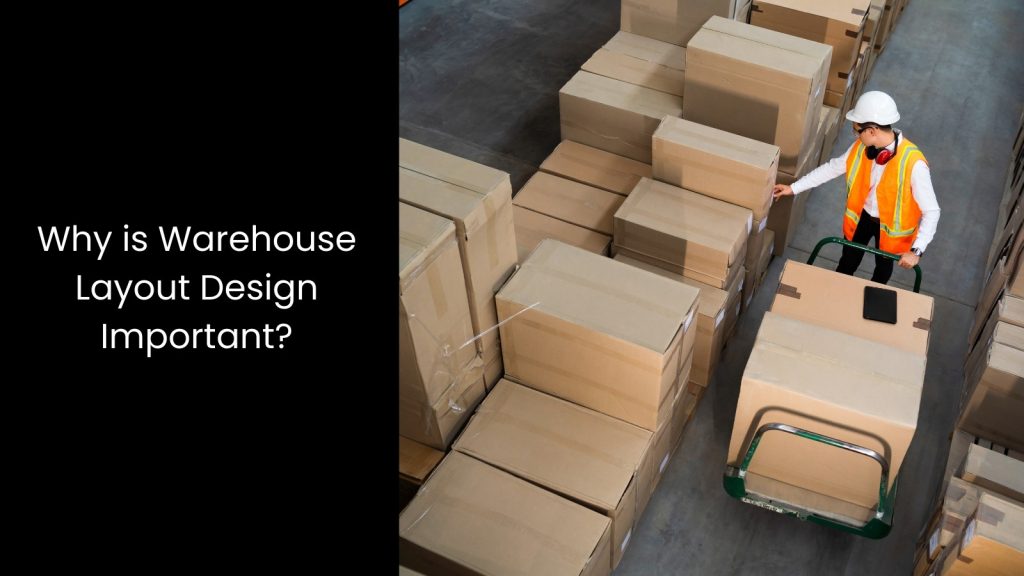
- Did you know that Singapore’s land area measures just 728 square kilometres, making efficient space use vital for businesses?
- A smart warehouse layout design is essential for any industry in Singapore, where every square meter counts. This layout directly impacts how effectively a warehouse can operate, ensuring businesses make the most of their limited space.
- A well-thought-out design organises storage zones, picking areas, and aisles to streamline workflows and improve efficiency. If the enterprises can plan these spaces carefully, they will be able to prevent wasted space, reduce travel time within the warehouse, and create a faster, more organised process for handling goods.
- An effective warehouse layout design also enables industries to manage inventory more accurately. When items have designated storage areas, workers locate products quickly, reducing errors and speeding up order fulfillment. For sectors like retail, e-commerce, and logistics, where rapid, accurate shipments are crucial, a clear and organised layout keeps operations smooth and customer satisfaction high.
- In Singapore’s competitive landscape, where space constraints are tight, businesses must design layouts that use vertical space, stacking inventory safely to maximise storage without expanding their footprint.
- The layout design also directly supports safety and productivity. When shelves, aisles, and picking zones are thoughtfully arranged, employees move quickly, and equipment operates safely, reducing accidents and preventing congestion.
Top 6 Tips for Optimising Space of a Warehouse Layout Design
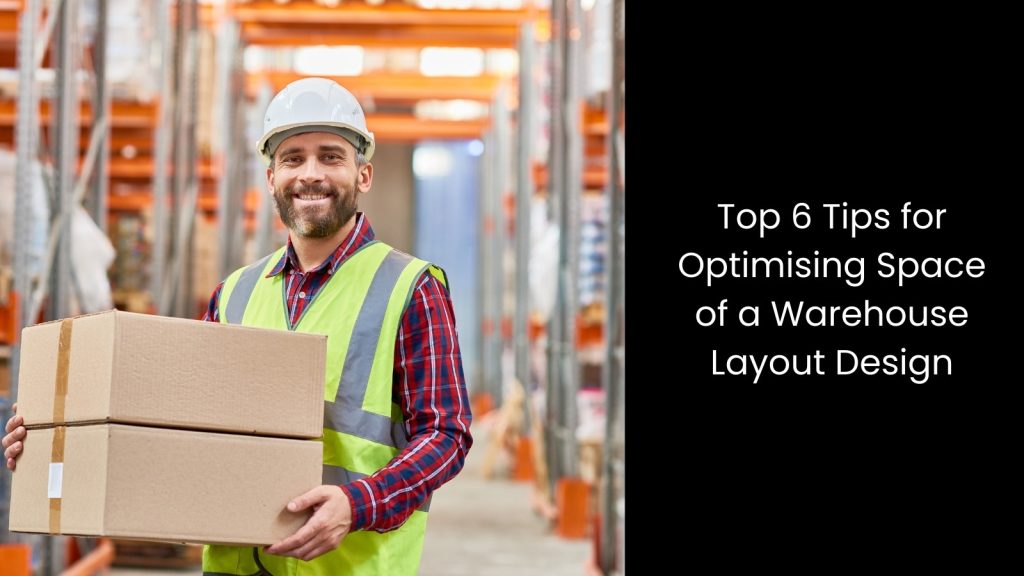
Analyse and Understand Your Workflow
Different industries rely on unique workflows, which makes understanding and analysing them essential for optimising warehouse layout design.
You know, industries such as retail, manufacturing, and e-commerce each follow specific processes, so a one-size-fits-all layout does not work. After analysing and understanding your workflow, you can tailor your warehouse design to fit your operations and maximise space efficiency.
You can start by assessing the flow of goods in your warehouse. Track how products move from receiving to storage, then to packing and shipping. Mapping these steps allows you to create a layout that reduces unnecessary movement, cuts handling time, and keeps everything organised.
For example, in an e-commerce warehouse, orders might require quick access to picking areas, while a manufacturing warehouse might need spacious zones for raw materials and finished products. When you align your layout with these needs, you speed up processes and reduce worker travel time. Placing high-demand items closer to packing stations or aligning shelves to allow direct access from storage to shipping zones helps streamline the process, making it faster and less prone to errors. You avoid crisscrossing paths and prevent bottlenecks, ensuring smoother movement throughout the warehouse.
Choose the Right Racking System
This plays a crucial role in optimising a warehouse design layout because it directly affects storage capacity, accessibility, and the efficiency of operations.
A well-suited racking mechanism lets you entirely use available space, especially vertical space, which is essential for maximising storage without expanding the warehouse’s footprint. Each warehouse has different storage needs, so you must select a racking system that matches your inventory type, picking methods, and movement of goods. For example, if you store large quantities of the same item, drive-in racks work well by allowing you to store products deep without aisles between every row. On the other hand, selective racks, which would enable easy access to each pallet, are better for warehouses with diverse products that need frequent picking.
Using the proper mechanism also improves your workflow by reducing the time spent locating and retrieving items. When you choose racks based on product demand and picking frequency, you can arrange them in zones that place high-demand items closer to picking and packing areas. This layout minimises travel time and speeds up order fulfilment.
Implement ABC Inventory Classification
This helps you organise items based on demand, ensuring faster access to high-priority products. Do you know what the ABC classification is?
If you do not, let us explain it to you. This divides inventory into three categories: A, B, and C. Category A includes high-demand items that are frequently picked or sold, and category B includes moderately popular items. Category C includes low-demand items that move slowly. You can strategically place items in your warehouse to improve efficiency by identifying these categories. Start by positioning category A items close to picking and packing areas since these products have the highest turnover.
This placement minimises the distance workers travel and reduces picking time, speeding up order fulfilment for popular items.
Category B items, which are moderately picked, work well in the middle areas of the warehouse, balancing accessibility with space efficiency. Finally, store category C items, which do not require frequent access, in the regions that are less convenient but still reachable.
When you use this arrangement, you make the best use of valuable storage space, keeping fast-moving products within easy reach and reserving less accessible space for slower-moving stock. This organisation not only saves time but also lowers operational costs by cutting unnecessary labour and reducing energy use in automated systems.
Incorporate Cross-Docking Areas
Cross-docking directly transfers incoming goods to outbound shipping without unnecessary storage, which helps reduce inventory costs and speeds up order fulfillment. This process allows warehouses to act more as transit hubs, where products are quickly sorted and sent to their final destinations.
When integrating cross-docking areas, warehouses can handle high-volume shipments with incredible speed and accuracy, benefiting operations dealing with perishable goods or items with high turnover rates. This approach also optimises space usage within the warehouse, freeing up valuable storage areas for other essential functions.
Warehouses with cross-docking areas reduce the risk of product obsolescence, as goods move swiftly through the facility and reach customers faster. This design also enables better organisation, separating inbound and outbound processes. Then, it leads to more efficient labour allocation and reduces the need for excessive handling, which minimises product damage risk.
Optimise Aisle Widths
This way, warehouses can ensure smooth and unobstructed paths for forklifts, pallet jacks, and other material handling equipment, allowing workers to navigate safely and quickly through the facility.
Wider aisles can enable faster loading and unloading of goods and reduce the risk of accidents, especially in high-traffic areas. However, optimising does not always mean widening; sometimes, reducing aisle width can increase storage density by creating more space for shelves and racks, which allows for more goods in the same footprint. Striking the right balance between accessibility and storage maximisation is essential to making the most of the warehouse space.
When optimising aisle widths, it is important to consider the types of vehicles used in the warehouse, as different equipment requires varying spaces to operate efficiently. For instance, narrow aisles may work best in warehouses using narrow-aisle forklifts or automated storage and retrieval systems, which allow for precise, high-density storage. Optimised aisle widths also help reduce the time employees spend retrieving items, boosting picking efficiency and improving order fulfilment speed.
Implement Suitable Technology
It is no longer a secret that top logistics companies around the globe rely on robust technology when it comes to space utilisation.
This is where software like Warehouse Management Systems (WMS) play a central role, as they help manage stock locations, track product movement, and guide workers to items quickly, which reduces time spent searching for goods and maximises available space. As it can analyse data, WMS software can also help determine optimal storage placements, ensuring high-demand items are accessible while maximising space for slower-moving stock.
This is the same with the RFID tracking systems. It takes this capacity further by providing real-time tracking of products, which enhances inventory accuracy and reduces errors, as each item’s location can be precisely identified.
Plus, warehouse sensors help monitor conditions like temperature and humidity, ensuring products are stored in optimal environments while avoiding overcrowded spaces. They also provide valuable data on movement patterns within the warehouse, enabling layout adjustments based on real-time insights. Another tool is Automated Guided Vehicles (AGV), which further improve warehouse layout by handling repetitive tasks such as transporting goods from one area to another. Not to mention that this would free up space by reducing the need for wide aisles and decreasing congestion in high-traffic areas.
Enhancing Warehouse Operations via Digital Platforms
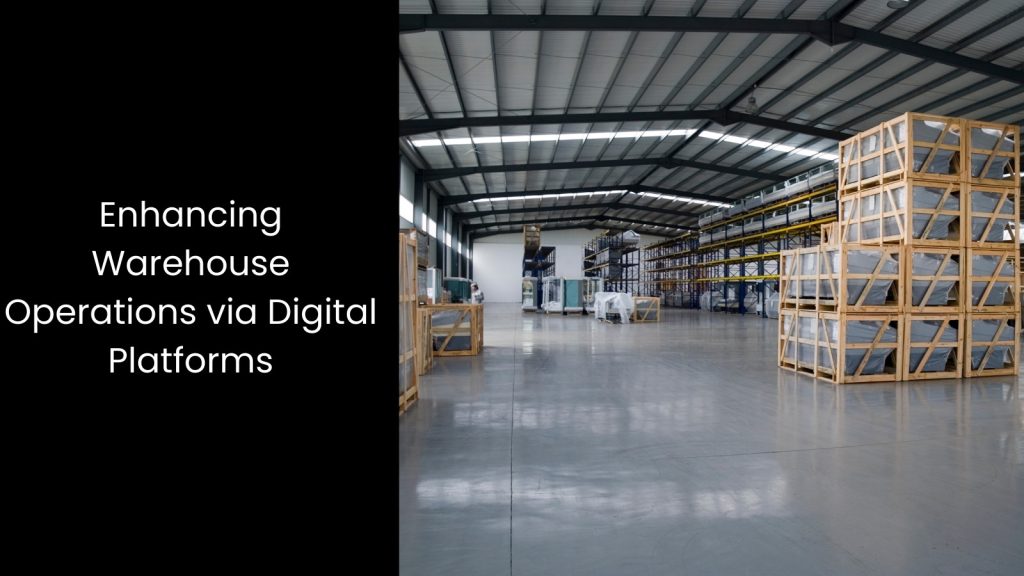
It is crystal clear that space is everything in warehouses. If you opt for a well-utilised layout, you will indeed change the game. A robust WMS from a reputed software partner can deliver this vision, making space utilisation more than just a strategy—it is the key to operational success and team satisfaction.