It is not a myth if we say that managing packaging inventory well can make a big difference for any business that deals with physical products. Whether you are handling boxes, wraps, labels, or fillers, keeping everything organised and easy to track helps you avoid delays and reduce waste. In a fast-moving market, efficient packaging inventory management matters more than ever.
This article shares key techniques to manage your packaging inventory smoothly, avoid common mistakes, and improve your packaging process.
We will explore
- Understanding Challenges in Packaging Inventory
- 12 Techniques to Manage a Packaging Inventory
- Conduct Regular Inventory Audits
- Implement Inventory Management Software
- Use Barcode or RFID Systems
- Set Minimum and Maximum Stock Levels
- Categorise Packaging Materials
- Apply the First-In, First-Out (FIFO) Method
- Forecast Demand Accurately
- Optimise Storage Space
- Integrate Packaging Inventory with Production Planning
- Train Staff on Inventory Best Practices
- Monitor Supplier Performance
- Implement a Continuous Improvement Strategy
- Top 5 Benefits of Efficient Packaging Inventory Management
- Using Robust Tools to Optimise Packaging Inventory Management
Understanding Challenges in Packaging Inventory
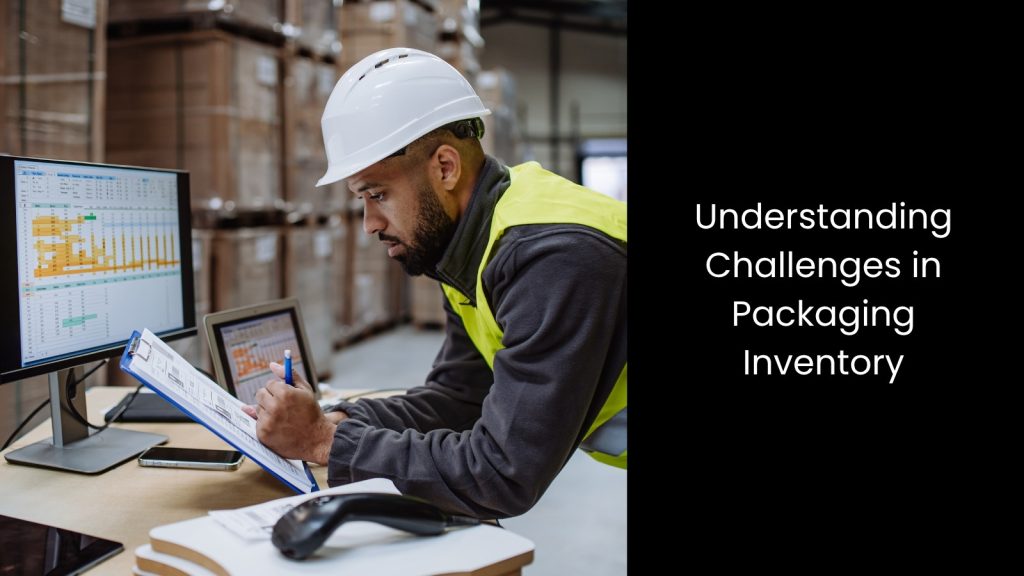
Stockouts
- Stockouts hurt your operations fast. When packaging materials run out suddenly, everything stops—production halts, shipping delays occur, and customers grow frustrated. You end up losing time, trust, and money. This kind of issue usually happens when no one tracks supply levels in real time.
Overstocking
- Overstocking creates a real headache in packaging inventory. When businesses order too much packaging material, they tie up money that could be put to better reuse. These supplies take up space and often go unused for long periods. Over time, boxes, labels, and wraps can get damaged, lose quality, or become outdated. This does not just waste resources; it adds to storage costs and complicates inventory counts.
Mismanagement
- When storage areas get messy or the wrong information enters the system, inventory becomes confusing and unreliable. You might think you have enough packaging, only to find out you do not. This mix-up leads to emergency orders, production delays, and higher costs.
12 Techniques to Manage a Packaging Inventory
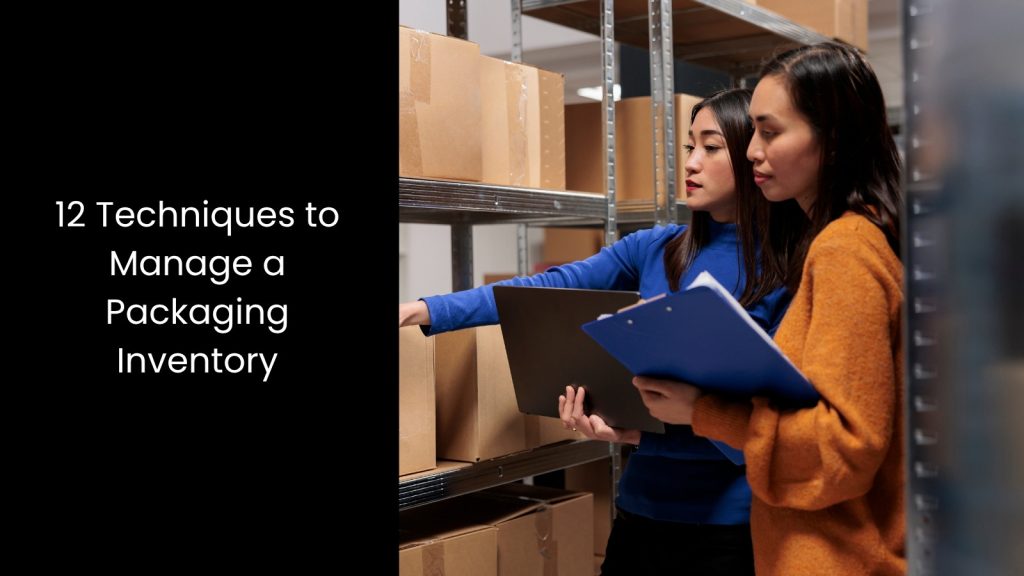
Conduct Regular Inventory Audits
When you perform routine packaging inventory audits, you catch problems early. You will spot missing items, fix numbers, and stop small mistakes from growing bigger. These checks help you keep a clear picture of what is in stock.
You can avoid both stockouts and overstocking when you match records with what is physically there. This habit also supports data-driven inventory decisions that keep your business running smoothly. People waste less, and you use shelf space better.
If you want effective packaging inventory management, always make time to check your stock. A clean record helps you control cost, boost supply accuracy, and reduce unwanted surprises.
Implement Inventory Management Software
If you want to manage packaging inventory effectively, then you need to switch to advanced inventory management software. Manual systems miss things, but packaging inventory software shows you what is going on in real time. These tools handle packaging inventory tracking, spot trends, and even automate packaging inventory tasks like reordering.
That way, you do not run out or buy too much. With the right packaging inventory tools, you can track boxes, wraps, labels, and fillers down to the smallest detail.
Use Barcode or RFID Systems
You cannot track items well without tech like RFID and barcode systems. These tags help scan and log packaging items instantly, cutting down on mistakes. Employees do not have to guess or double-check long lists anymore.
Instead, they use packaging inventory technology that scans items in and out with a beep. This speeds up inventory count and tracking while reducing mix-ups. You also cut out human error, which often causes packaging inventory challenges.
Therefore, if you want an efficient packaging inventory, get your labels, codes, and scanners working together.
Set Minimum and Maximum Stock Levels
When you set reorder levels, you stop surprises before they hit. Minimum stock keeps you from running out, while maximum stops you from stuffing your storage.
Your warehouse people do not have to guess how much to order; they follow clear limits. These levels help control packaging inventory optimisation, so shelves are not too full or too empty. You can also match stock with usage, cutting down on waste.
In the long run, this keeps your packaging inventory system stable and more predictable. Whether you manage packaging materials for e-commerce or in bulk, having set boundaries makes your supply chain smarter and faster.
Categorise Packaging Materials
Grouping items like boxes, wraps, labels, and fillers based on size, usage, or type makes things easy to find. Teams grab what they need without digging through clutter. Sorting your stock supports packaging inventory optimisation and leads to faster packing and shipping.
Furthermore, if you want efficient packaging inventory, make categories that match how your team works. This simple step also helps your packaging inventory tracking system stay more accurate.
Apply the First-In, First-Out (FIFO) Method
Old packaging can lose quality. Using the FIFO method means you use older stock before opening newer ones.
This keeps packaging fresh and avoids throwing out materials that degrade over time. Inventory handlers can place new deliveries at the back and grab older stock from the front. This method helps cut packaging inventory waste and supports sustainable packaging practices.
Plus, FIFO keeps your rotation clean and reduces clutter, too. When you follow this rule, your packaging inventory management becomes cleaner and smarter.
Forecast Demand Accurately
Guessing demand can break your flow. Instead, you can use inventory forecasting to study past sales and usage trends. Did you know this?
Teams that read the numbers know what is coming and plan their packaging material usage patterns better. This helps avoid stock build-up and keeps reordering steady. With accurate predictions, you cut costs and reduce emergency buys. Forecasting fits into strong packaging inventory strategies because it gives your system rhythm and flow.
Optimise Storage Space
When you optimise storage, your team grabs what they need faster. Use clear labels, stackable bins, and smart layouts that match how your team works.
Don’t let packaging supplies take up more space than needed. This helps reduce handling time and supports smoother tracking. Efficient packaging storage solutions also prevent damage to materials. You save space, money, and effort in one go. Good layouts make packaging inventory management smoother and help you scale more easily.
Integrate Packaging Inventory with Production Planning
Your packaging inventory system should not run separately from production. Sync both together to stay on track. When production needs match your stock levels, everything flows better. Teams plan ahead, order materials just in time, and avoid delays.
Linking packaging supply with production reduces mistakes, especially when you manage multiple product lines. This step helps avoid packaging inventory challenges and supports smoother workflows. Integration also works great with e-commerce platform integration, so that online orders trigger automatic packaging prep.
Train Staff on Inventory Best Practices
Even the best tools cannot fix mistakes if your team does not know what to do. This is why you need to train staff on how to handle, label, and record packaging stock correctly.
A well-informed team keeps your packaging inventory tracking system clean and clear. Teach them to spot errors early, follow FIFO, and respect reorder levels. Good habits cut losses and improve accuracy across your whole packaging inventory management setup.
Monitor Supplier Performance
If your supplier messes up, your system suffers. Track things like how fast they deliver, the condition of goods, and how often they get it right. Strong supplier relationships support a stable supply.
Keep backup suppliers ready so you do not get stuck. When you monitor suppliers, you improve your packaging inventory tracking because you know when and what to expect. It is easier to plan reorders, avoid delays, and stay ready for busy seasons.
Implement a Continuous Improvement Strategy
You need to remember one thing: never stop improving your system. Review what works, talk to your team, and make small fixes often.
You do not need big changes, just smart updates. Try lean methods, clear processes, and better layouts. Track your inventory performance indicators (KPIs) to spot weak areas. Use what you learn to adjust and grow. This supports long-term packaging inventory optimisation and helps avoid repeating old mistakes.
As markets shift, your system stays flexible. Teams feel more confident, and your packaging inventory management gets stronger with each update.
Top 5 Benefits of Efficient Packaging Inventory Management
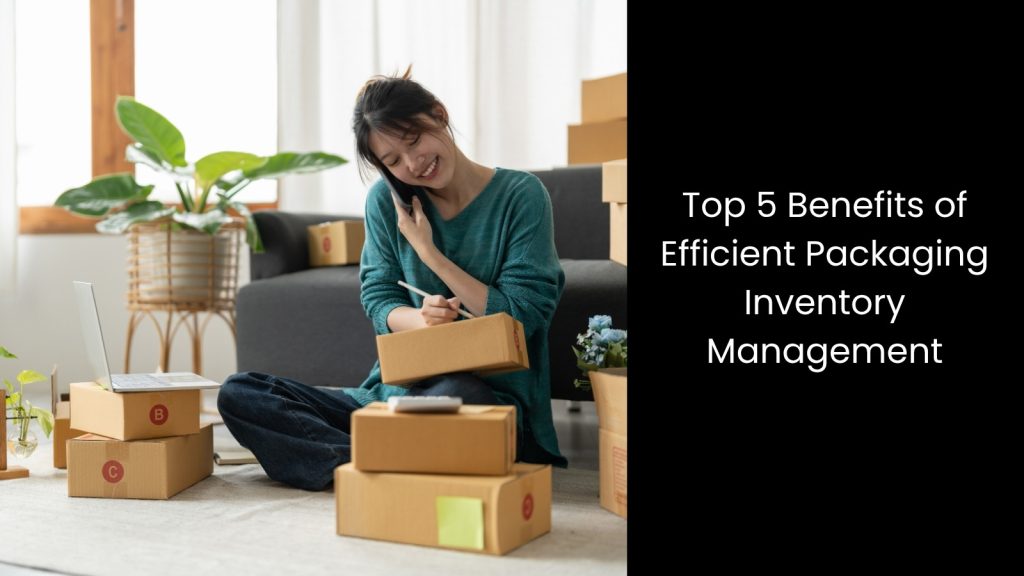
Stronger Supplier Bonds through Real-Time Inventory Tracking
When teams use real-time inventory data and a good packaging inventory tracking system, they share information faster with suppliers. This improves supplier relationships, builds trust, and keeps the packaging supply chain moving without delays or surprises.
Smoother Operations with Packaging Inventory Optimisation
Running an efficient packaging inventory process means fewer delays, fewer headaches, and better decisions. It also helps you avoid mistakes, improve workflows, and make sure you never get caught off guard with stockouts and overstocking.
Saving Money with Smarter Packaging Inventory Strategies
You save more when you manage packaging materials right. Good packaging inventory optimisation avoids waste, lowers extra storage costs, and frees up cash. This money then goes into marketing, tech, or growth plans instead.
Making Smarter Choices Using Data-Driven Inventory Decisions
With the help of advanced inventory management software, you can read into usage trends and performance. The system shows clear inventory performance indicators, letting you act fast and plan smarter using packaging inventory analytics.
Eco-Friendly Gains with Sustainable Packaging Practices
You build greener systems when you avoid waste and optimise storage space. Efficient packaging inventory management supports sustainable packaging practices, which modern brands value as part of their mission to protect the planet.
Using Robust Tools to Optimise Packaging Inventory Management
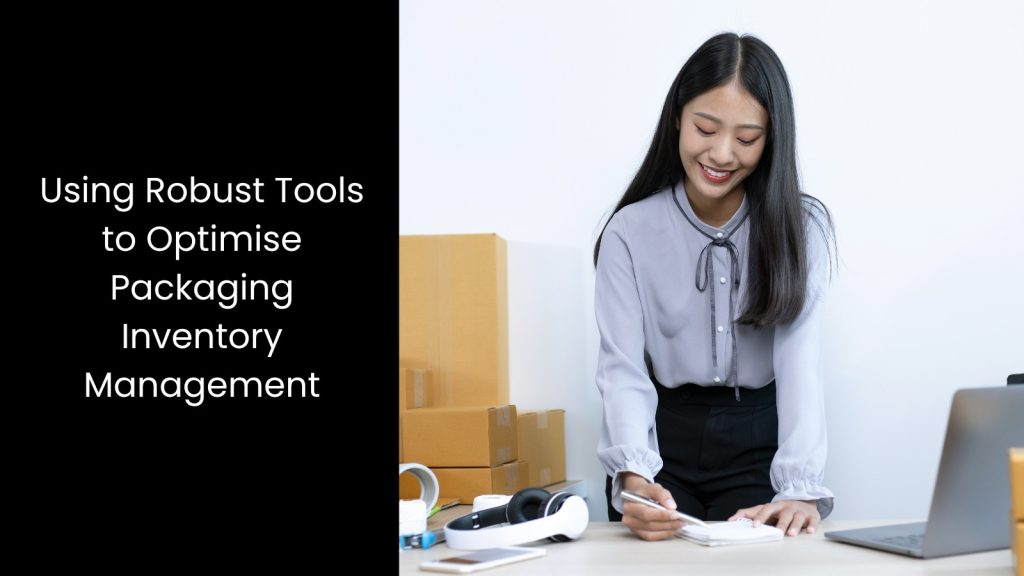
You may understand that packaging mistakes cost time, money, and customer trust. But when you manage your packaging inventory using advanced Warehouse Management Software, you stay ahead of challenges. With features like RFID systems, usage trend tracking, and alerts for reorder levels, you make better decisions faster. To grow without chaos, invest in tools developed by an industry expert that keep your packaging inventory smart, lean, and ready for any demand.